
PART 2: THE SIX MUST-HAVE ELEMENTS IN STANDARD OPERATING PROCEDURES
PART 2: THE SIX MUST-HAVE ELEMENTS IN STANDARD OPERATING PROCEDURES
Remember when your English teacher introduced the idea of an introductory paragraph? She said you need to include certain information to help the reader immediately identify what your essay or story is about. And what made that lesson so memorable was the inclusion of Who, What, When, Where, and Why.
All those W’s stuck in your brain. Well, those W’s are going to help you in writing Standard Operating Procedures (SOPs) as well. But this time, we’re also going to add an H with “How.”
“How” turns out to be the most important of the six, but we’ll get to that later. Here’s the list of key elements along with the questions they should answer.
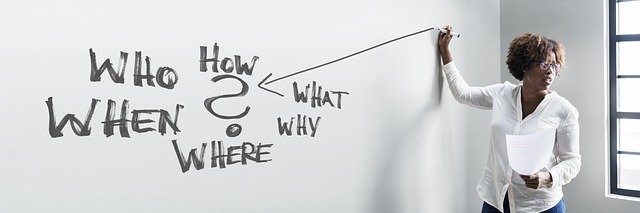
“Front Matter”
Where?
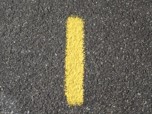
Title Page and/or Header. The title page should clearly indicate where the operating procedures are performed. The “where” might simply refer to the department in which the procedure is followed.
Of course, some companies have multiple locations. Each location may have different functions within the larger company, so each location will develop its own SOPs.
Some companies may have multiple locations performing the same operations, but they would likely still need separate SOPs. For example, the machinery and hardware at one location might be older than the other locations’ hardware, and more aggressive inspections at more frequent intervals might be required.
Additional items on the Title Page and/or Header:
- The name of the document
- The approval date or date of revision and revision number
- The document number
What?
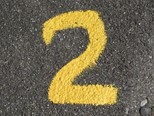
a. Scope. The scope identifies the process to be addressed and which activities are included. An SOP focuses on a single repetitive process or routine procedure.
Your company should have multiple SOPs, but each should be limited to its own document.
Scope-Safety Culture suggests that, in addition to defining the process or procedure in the document at hand, you may need to define what is not addressed and refer the reader to another document.
For example, you have an SOP for required housekeeping procedures for the craftsmen in your shop. In 2020, you needed an SOP to capture housekeeping procedures during a global pandemic. If so, the Scope section of each document should state that the SOP does not include the requirements contained in the other document, and it should refer the reader to that document.
b. Quality Assurance. After identifying the exact procedure your SOP will cover, you should address the way in which the procedure will be monitored for quality.
Identify the method, actions, or inspections that will serve as quality control for your product, service, system, or process. Will your product undergo testing by an independent lab? Will your customer service calls be recorded and monitored by a supervisor? Will there be inspections or monthly audits? It is important for employees to be aware from the outset that the results of their efforts will be evaluated.
When?
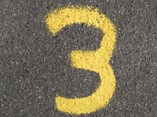
Schedule. Are the steps in this SOP to be performed daily, weekly, monthly, or semiannually? Are there inspections to performed at less frequent intervals? If so, these intervals must be clearly defined.
Perhaps these steps occur when a certain situation arises. For instance, your SOP may be about certain situations in customer service, such as the steps in deescalating customer frustration about particular issues.
Your SOP might also outline the repair of machinery or equipment when there is a malfunction or damage. The situation in which the procedures are to be implemented must be clearly defined as well.
Why?
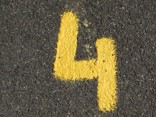
Purpose. We’ve talked about the importance of SOPs and the ramifications of not having them. So, this section is where you tell your employees why it’s important to the company and why it should be important to them. Is its purpose to make clear to everyone in a particular department or group what to do and what tasks are mandatory? Is it for the employee’s personal safety and the safety of their coworkers?
Is it for workers in the field whose actions impact smooth operations and the safety of personnel and equipment?
Who?
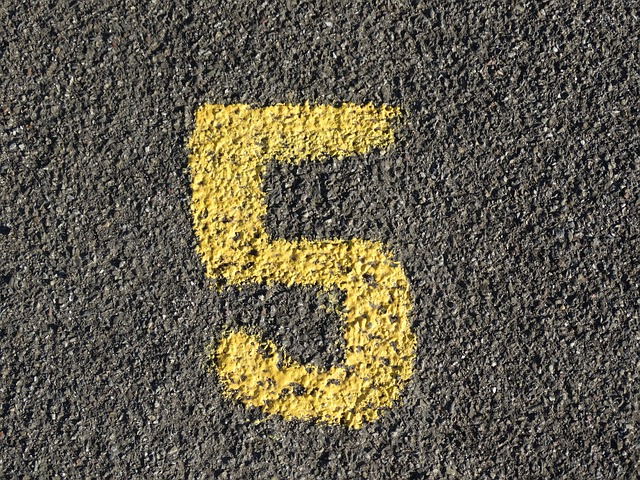
Responsible Parties. This section identifies the group of employees who will perform the actions, such as workers in a particular office, members of a particular trade, etc. This section also identifies and anyone who bears responsibility when those actions are not followed or when a situation arises that needs special attention. This includes foremen, supervisors, inspectors, and managers.
Optional, but Potentially Critical Elements of “Front Matter”
Acronym Lists.
For short documents and documents that use the same acronyms throughout the document, it suffices to define the acronym upon first use (spell out each word and follow them with the acronym in parentheses) and use the acronym thereafter.
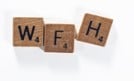
In an SOP, it’s more likely that there are a significant number of pages between an acronym’s first use and subsequent usage. If that’s the case, the reader will probably forget what it means. That may spark a lengthy hunt for where it was first mentioned.
If the document has a more than a few acronyms, a new employee may have difficulty keeping up with them. So, it’s helpful to have a separate list of acronyms.
List of Definitions.
Some businesses place key importance on certain words. These words may take on meanings and nuances that are specific to the company or the industry. For example, in companies guided by the Occupational Safety and Health Administration (OSHA) safety guidelines, there are “incidents” and “accidents.” To a new employee, these may sound interchangeable, but they are not.
A list of definitions will include the industry-specific meaning and what distinguishes the term from other words that seem to be synonymous. Senior Project Manager Michael McBride, who formerly managed SOP development at a major engineering technical professional services firm, provided his insight for this article. McBride says simply, “The List of Definitions should include any meanings beyond Webster.”
Not surprisingly, OSHA lists the following words as candidates for inclusion in SOPs: Risk, Personnel, Consequence, Summative assessment, and Work Control Plan (WCP).
Does your business have words that make a difference in your workplace?
The Meat: The Body of the Document
How?
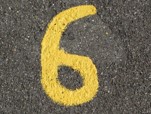
Steps. Of the five sources consulted for this article, four used the word “unambiguous” to describe the language to use in the steps in an SOP. An example of “unambiguous” is the use of certain words, including shall, should, must, and may.
The FDA Group points out that using the word “may” gives personnel decision-making power and/or flexibility, and “must” is always mandatory.
Shall and should work the same way. While “shall” is mandatory, “should” is used when noncompliance is permissible under certain circumstances.
McBride emphasized that the explanation as to when deviations/noncompliance are permissible should be described within the steps themselves. He stressed that deviations must be addressed in detail:
- When might it be ok to deviate from the procedure?
- Exactly what are the circumstances?
- What form or forms might be required?
- Who approves the deviation?
Use “shall” and “should” to precede your steps.
You should:
1: Number your steps.
2: Start each step with a verb.
3: In instances where there is a phrase that helps qualify the actions in the step, begin the sentence with that phrase. For example: “If there is any obstruction in the line, clear the obstruction before you proceed.”
- If there is an SOP for clearing the line, refer to that SOP.
- If the method is simple, provide the steps beneath—indented in outline fashion.
4: Keep it simple. Use language that is easily understood.
5: Be consistent. If you mean the same thing, say it the same way.
Qualifications.
McBride suggests that the required qualifications for the individuals performing the tasks should be included after the steps that they are to perform. This is so that the employee understands the responsibilities they will have after earning the required designation. Perhaps, after reading what the foreman does, they may decide not to go that route. Alternately, Qualifications may be included in the section called Responsible Parties.
Often Included at the End
Checklists.
Checklists are often included at the end of an SOP. They may be for employees to use to ensure that they perform their tasks according to steps outlined in the SOP. Others may be used by supervisors, managers, or inspectors in their QA checks.
In its Guidance for Preparing SOPs, EPA.gov reminds readers that these checklists are NOT the SOP. They are included for reference. Often the checklists included are marked “For reference only” or with the watermark “SAMPLE.” Checklists are often modified more often than the SOP is updated. It’s critical that employees use the latest version of the checklist available from either their supervisor or an electronic storage system accessible to employees.
What’s the Key to Clarity, Synergy, and Compliance?
Accessibility.
The EPA says it best in its Guidance for Preparing Standard Operating Procedures:
“Current copies of the SOPs . . . need to be readily accessible for reference in the work areas of those individuals actually performing the activity, either in hardcopy or electronic format. Otherwise, SOPs serve little purpose.”
This means you will need a system for document storage that ensures employees are operating according to the latest version of each procedure.
A Note about Hardcopies.
A document control system ensures that the most recent version of each document is available. However, once printed, there’s no control. The employee who prints the procedure, keeps it in their desk, and pulls it out for reference a month or two later runs the risk of operating from checklist or a set of procedures that has been revised. The sooner your company is able to provide a system that enables employees to view procedures in an electronic format in the work area the better.
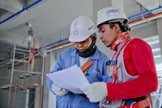
The Occupational Safety and Health Administration (OSHA) recommends including “Uncontrolled when printed” in the footer.
So Much To Do!
You may be:
- Starting a small business,
- Or a new manager facing the challenge of getting a division of employees to adopt new processes,
- Or someone whose company is coping with inventory shortages, product quality issues, or accidents in the shop.
You’ve got a LOT on your plate!
Words like “must-have,” “up-front effort,” “stakeholder team,” “document control system,” “written procedures” and the idea of having hardware or devices to provide employee access in every work area may be daunting—even overwhelming. You know that it makes perfect sense, and you know it must all be done, but you may simply be spread too thin.
Bringing in a team of professionals to interview key stakeholders and draft the SOPs can relieve you of a lot of the burden. You can leave the team meetings and the review and approval process to your key stakeholders and the writing professionals. Then you simply review the document for final approval.
Related Content
- 0 Comment
Subscribe to Newsletter
- How Can SharePoint Be Used To Organize and Disseminate SOPs?
- Planning the Perfect Genealogy Research Trip: A Step-by-Step Guide
- From Silly to Awesome: How Words Change Meaning Over Time
- The Psychology of Font Choice: How Typography Impacts Content Engagement
- How to Distribute SOPs for Maximum Usability